3 Common Mistakes to Avoid When Using an Air Impact Wrench
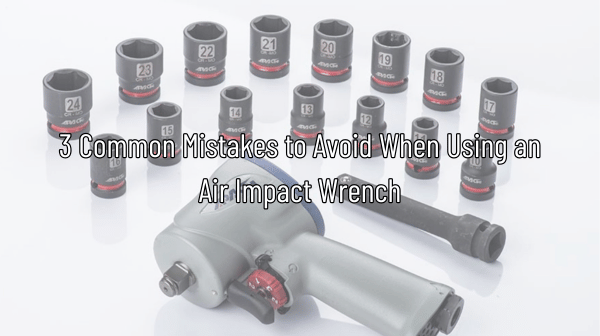
An air impact wrench, also referred to as a pneumatic impact wrench or impact gun, is an essential tool in automotive, industrial, and construction applications. Its ability to deliver high torque with minimal effort makes it a favorite among professionals. However, improper use can lead to inefficiencies, damage to tools or fasteners, and even safety hazards. To get the most out of your air impact wrench, it's important to avoid these common mistakes.
1. Using the Wrong Torque Setting
One of the most frequent mistakes is applying too much or too little torque. Over-torquing can strip threads, damage fasteners, or even crack the materials being worked on. Under-torquing, on the other hand, may leave bolts loose, compromising the structural integrity of the project.
How to Avoid This Mistake:
- Check the torque specifications for your project before starting.
- Use a torque stick or a calibrated torque wrench for precise settings, especially for critical applications like engine work or wheel lugs.
- Regularly maintain your air impact wrench to ensure consistent torque delivery.
2. Improper Air Pressure
An air impact wrench relies on compressed air to generate the power needed for high-torque applications. Using the wrong air pressure can lead to inefficient performance or even tool damage. Operating at too low a pressure reduces the tool's effectiveness, while excessive pressure can strain internal components and shorten the tool's lifespan.
How to Avoid This Mistake:
- Always check the recommended air pressure for your impact gun, typically between 90 and 120 PSI.
- Use a properly regulated air compressor to maintain consistent pressure.
- Regularly inspect hoses and connectors for leaks that can reduce air pressure.
3. Neglecting Tool Maintenance
Like any tool, an air impact wrench requires regular maintenance to function optimally. Neglecting maintenance can lead to reduced performance, increased wear and tear, and costly repairs or replacements.
How to Avoid This Mistake:
- Lubricate your air impact wrench daily or as recommended by the manufacturer. Use air tool oil to keep internal components running smoothly.
- Clean the tool after each use to remove dirt, dust, and debris.
- Check and replace worn parts, such as O-rings or impact sockets, to prevent malfunctions.
- Drain your air compressor regularly to avoid moisture buildup, which can damage the tool’s internal components.
Bonus Tip: Use the Right Tool for the Job
Not all air impact wrenches are created equal. Using the wrong size or type of wrench can lead to inefficiencies and potential damage. For example:
- A 3/8" drive is better suited for light-duty tasks.
- A 1/2" drive is versatile and works well for most automotive and general tasks.
- Larger drives, like 3/4" or 1", are meant for heavy-duty industrial applications.
At Apach, we offer a variety of air impact wrenches with different drive sizes and features, including stubby types for tight spaces and special patent designs for enhanced performance.
Conclusion
By avoiding these common mistakes—misusing torque settings, operating at improper air pressure, and neglecting maintenance—you can maximize the efficiency, longevity, and safety of your air impact wrench. Whether you’re an automotive professional or a construction worker, taking these precautions will help you achieve the best results.
Looking for reliable air impact wrenches? Explore our selection at Apach and find the perfect pneumatic impact wrench for your needs. Contact us today for expert advice and support!
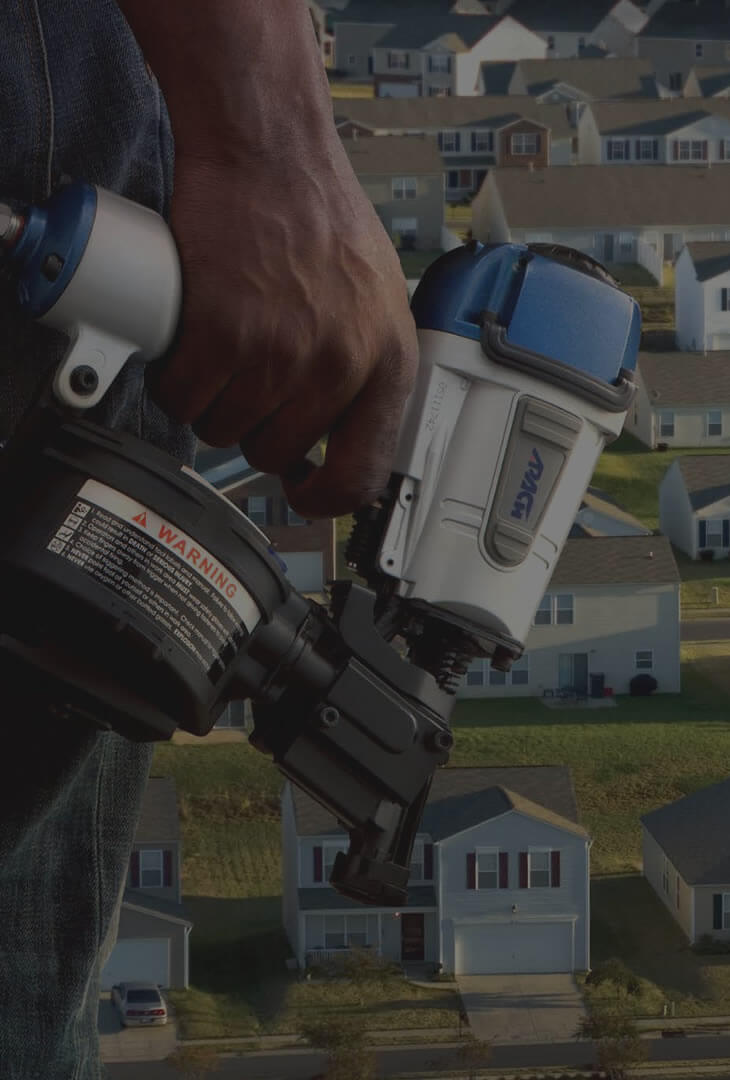